You’ll find three clear market leaders dominating today’s prefabricated small house manufacturing: Berkshire Hathaway Inc. ($5.57B revenue), Cavco Industries ($1.73B), and Skyline Champion ($1.39B). Each offers distinct advantages in construction speed, quality control, and customization options. Their factory-based production delivers up to 90% waste reduction compared to traditional building methods, while maintaining profit margins between 8.9-12.8%. A deeper analysis reveals how these manufacturers are reshaping housing’s future through innovation and sustainability.
Key Takeaways
- Berkshire Hathaway dominates the prefab market with $5.5B revenue, followed by Cavco Industries at $1.7B and Skyline Champion at $1.3B.
- Skyline Champion leads in profit margins at 12.8%, outperforming both Cavco Industries (9.2%) and Berkshire Hathaway (8.9%).
- Manufacturers offer diverse customization options, from entry-level models starting at $90,000 to premium hurricane-resistant and energy-efficient designs.
- Factory-based production reduces construction time to weeks while maintaining strict quality controls and regulatory compliance.
- Top manufacturers integrate eco-friendly materials and smart technology, achieving 90% less waste compared to traditional construction methods.
Market Leaders and Their Manufacturing Approaches
Several industry giants dominate today’s prefabricated small house market, with Berkshire Hathaway Inc. leading the pack at $5,571.2 million in projected revenue. Their 8.9% profit margin reflects their focus on high-quality, customizable housing solutions that you’ll find competitive in the current market.
The market leaders employ distinct manufacturing approaches to maintain their edge. Cavco Industries Inc.’s strategy centers on affordable solutions, generating $1,732.2 million in revenue with a 9.2% margin. You’ll notice Skyline Champion Corporation’s different approach, emphasizing innovative, energy-efficient designs that command a 12.8% profit margin on $1,390.1 million in revenue.
The industry’s seeing significant consolidation, as demonstrated by Champion Enterprises’ merger with Skyline. This trend’s forcing smaller manufacturers to exit as larger companies leverage economies of scale to maintain margins despite rising costs. You’ll find this concentration helps market leaders achieve lower costs while maintaining product quality and customization options.
Design Innovation and Customization Options
You’ll find that today’s prefabricated small houses offer numerous modular style adaptations that transform based on your living requirements, from stackable multi-family configurations to storm-resistant single units. Your space-saving options integrate seamlessly with customizable floor plans that maximize every square foot through built-in storage solutions and multipurpose areas. The systems-based approach to these designs allows you to select specific features that match your lifestyle needs while maintaining the structural integrity and efficiency of prefabricated construction methods.
Modular Style Adaptations
Modern modular homes have revolutionized the concept of personalized living spaces through innovative design adaptations. You’ll find that manufacturers now offer stackable configurations that comply with building codes while maximizing spatial efficiency. Companies like Zeni Homes demonstrate this through their multifamily solutions, which you can customize to meet specific urban planning requirements.
You can select from various architectural styles that integrate eco-friendly materials and energy-efficient systems. Deltec Homes exemplifies this adaptability by offering hurricane-resistant designs that don’t compromise on sustainability. Whether you’re interested in DIY assembly or professional installation, today’s modular homes provide flexible solutions that accommodate your specific needs. The industry’s shift towards customizable components means you can create living spaces that reflect both your aesthetic preferences and functional requirements.
Space-Saving Design Features
While space constraints present distinct challenges in prefabricated housing, innovative design features have transformed compact living into an art of efficiency. Leading manufacturers of manufactured homes now integrate sophisticated space-saving design features that maximize functionality without compromising comfort.
You’ll find these essential space-optimization elements in modern prefabricated homes:
- Multi-functional furniture systems that adapt to your changing needs throughout the day
- Open floor plans with modular wall configurations that enhance natural light distribution
- Smart home technology integration that reduces physical control panels and enhances space utility
- Energy-efficient design elements that combine space conservation with reduced utility costs
These innovations reflect manufacturers’ commitment to delivering compact yet highly livable spaces that align with contemporary lifestyle demands while maintaining structural integrity and system efficiency.
Construction Speed and Quality Standards
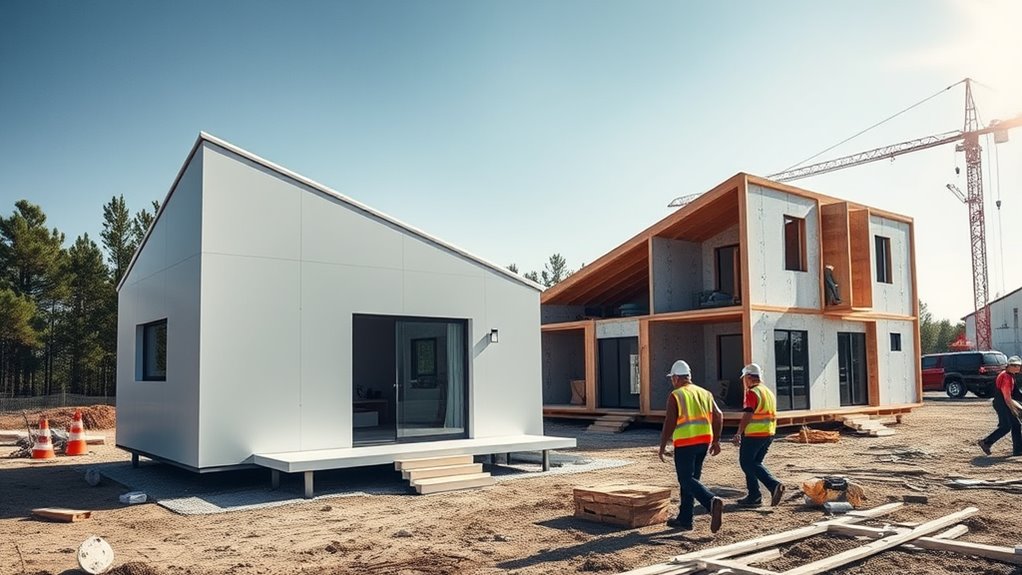
Despite their rapid construction timeline, prefabricated small houses consistently meet or exceed traditional building standards through their factory-controlled assembly process. You’ll find that leading manufacturers like Skyline Champion and Cavco Industries complete units in weeks rather than months, while maintaining rigorous quality control protocols in their climate-controlled facilities.
The controlled factory environment notably reduces construction errors and weather-related delays, ensuring consistent quality across all builds. You can customize your home with high-grade materials and finishes without compromising the accelerated build schedule. Companies like Deltec Homes demonstrate how prefab construction achieves superior structural integrity, particularly in hurricane-prone regions, through standardized manufacturing processes.
When you choose a prefabricated home, you’re getting the dual benefit of rapid construction speed and enhanced quality standards that often surpass local building codes. This combination of efficiency and excellence makes prefab housing an increasingly attractive option for homeowners seeking reliable construction methods.
Environmental Impact and Sustainability Features
You’ll find that prefabricated small houses incorporate eco-friendly building materials like recycled steel, sustainably harvested wood, and low-VOC components throughout their construction systems. Your energy consumption decreases through integrated features such as advanced insulation systems, solar-ready roofing, and smart climate controls that optimize heating and cooling efficiency. The factory-based production process enables precise material calculations and standardized waste sorting protocols, resulting in up to 90% less construction waste compared to traditional on-site building methods.
Green Building Materials Used
In the pursuit of environmental sustainability, prefabricated small houses incorporate a range of eco-friendly materials and features that minimize their carbon footprint. You’ll find that manufacturers prioritize green building practices through careful material selection and innovative construction techniques.
Key sustainable materials implemented in these structures include:
- Reclaimed wood sourced from demolished buildings or sustainably managed forests
- Recycled steel components that reduce the demand for new metal production
- Low-VOC paints and finishes that improve indoor air quality
- Insulated panels and energy-efficient windows that optimize thermal performance
These materials align with recognized green building standards like LEED certification, while the factory-based construction process guarantees precise material utilization, minimizing waste. The combination of sustainable materials and controlled manufacturing creates homes that are both environmentally responsible and resource-efficient.
Energy Consumption Reduction Methods
Modern prefabricated small houses employ three primary energy consumption reduction methods that considerably lower their environmental impact. You’ll find integrated energy-efficient designs featuring advanced insulation systems and strategic window placement to maximize natural lighting and temperature control. The homes incorporate sustainable materials, including reclaimed wood and low-VOC paints, which reduce both construction waste and long-term environmental impact.
The most significant energy reductions come from smart technology integration. You can expect built-in solar panels working in tandem with energy-efficient HVAC systems, creating a thorough energy management solution. Leading manufacturers like Deltec Homes have optimized these systems to withstand extreme weather while maintaining peak efficiency. These features align with federal initiatives promoting energy-efficient housing, ensuring you’ll benefit from both reduced utility costs and enhanced environmental sustainability.
Waste Management During Production
While traditional construction methods often generate substantial waste, prefabricated small houses drastically reduce environmental impact through systematic waste management protocols during production. You’ll find sustainability at the core of modern prefab manufacturing, where environmentally friendly practices optimize resource utilization in controlled factory settings.
- Material pre-cutting and precise assembly processes minimize excess waste generation
- Integrated recycling programs guarantee proper handling and repurposing of production byproducts
- Factory-controlled environments enable efficient material storage and inventory management
- Government-mandated sustainability requirements drive continuous improvement in waste reduction
These streamlined approaches mean you’re investing in a home that supports environmental conservation. Manufacturers like Deltec Homes demonstrate how systematic waste management not only reduces landfill impact but also creates cost efficiencies that benefit both producers and homeowners through optimized resource allocation.
Cost Analysis and Value Proposition
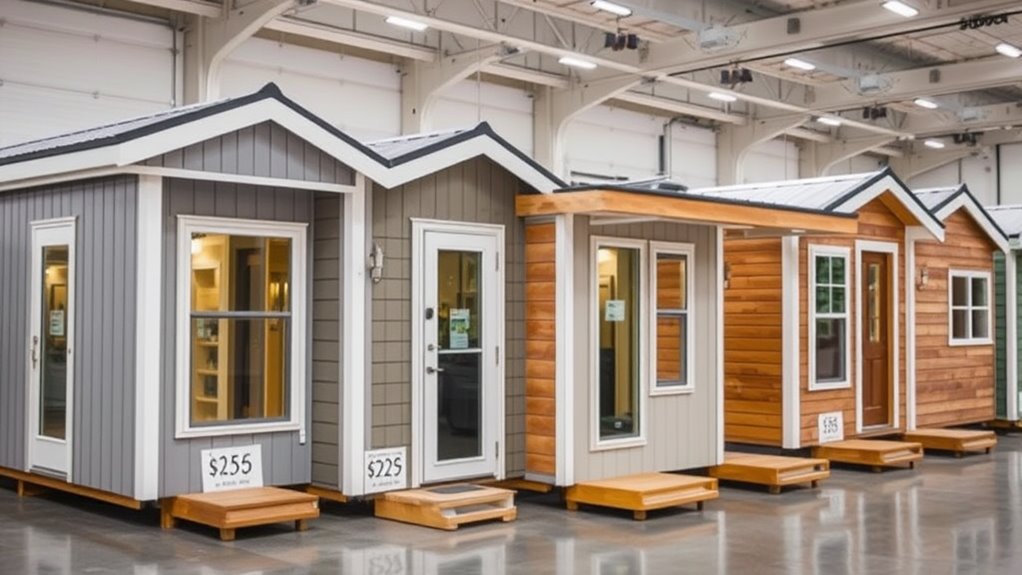
Despite common misconceptions about prefabricated housing being a budget-only option, today’s market reveals a complex cost structure that spans from affordable manufactured homes to premium modular designs. You’ll find entry-level options from companies like Zeni Homes starting at $90,000, while specialized manufacturers like Deltec Homes command higher prices for their hurricane-resistant, energy-efficient models.
The value proposition becomes clearer when you examine industry metrics. Leading manufacturers maintain healthy profit margins – Skyline Champion at 12.8% and Cavco at 9.2% – while delivering quality homes faster than traditional construction methods. Government support through the Prefabricated Housing Act strengthens this proposition by potentially reducing consumer costs. Your investment in a prefab home can yield significant returns through reduced construction time and energy efficiency, particularly in areas facing housing shortages. The manufactured mobile home segment continues to dominate the market, offering the most competitive price points without sacrificing essential features.
Regulatory Compliance and Industry Certifications
Confirming compliance with federal regulations remains a cornerstone of the prefabricated housing industry, where manufacturers must navigate complex regulatory frameworks established by HUD and the ICC. You’ll find that regulatory compliance involves meeting strict standards for safety, durability, and energy efficiency, while industry certifications from organizations like MHI validate these requirements.
To maintain compliance and certification standards, manufacturers must:
- Submit their designs for third-party inspections to verify adherence to building codes
- Implement quality control systems that meet HUD’s manufacturing standards
- Obtain necessary certifications from recognized industry organizations
- Document compliance with the Prefabricated Housing Act guidelines
When you’re evaluating prefabricated small houses, it’s essential to verify that manufacturers have obtained proper certifications. These credentials demonstrate their commitment to quality and guarantee they’re meeting federal requirements, ultimately protecting your investment and assuring the structural integrity of your prefabricated home.
Conclusion
As the old saying goes, “measure twice, cut once,” and you’ll find this wisdom applies perfectly to prefab home selection. You’ve now seen how leading manufacturers differentiate through production methods, design flexibility, and sustainability metrics. By evaluating construction timelines, quality controls, and certification standards systematically, you can determine which manufacturer’s specifications and systems align best with your residential requirements.